Puntlassen van aluminium en aluminiumlegeringen
Door: A.J. Schornagel
De oppervlaktetoestand van aluminium plaat is een van de belangrijkste beslissende factoren bij het verkrijgen van een consistente kwaliteit van de weerstandspunt- en bandlassen. Variaties in de dikte van de oxidelaag zullen van invloed zijn op de weerstand tussen beide elektrodes en de platen en aan het grensvlak tussen de platen. De weerstand kan worden gemeten door een enkele plaat tussen twee elektrodes te klemmen en een stroom ter grootte van 10 - 15 A door te sturen, waarbij de spanning wordt gemeten, zodat met behulp van de wet van Ohm (R = E/I) de weerstand kan worden berekend. Materiaal in de leveringstoestand kan een weerstand hebben oplopend van 300 microohm tot verscheidene miljoenen micro-ohm. Gereinigde en voorbereide plaat dient een weerstand te geven van 10 - 100 micro-ohm. Voor de hoogste en meest consistente kwaliteit kan dit interval nog worden versmald tot 10 - 30 micro-ohm. Mechanisch gereinigde oppervlakken leveren doorgaans een langere standtijd van de laselektrodes dan chemisch gereinigde oppervlakken, waarbij gefreesde oppervlakken de kortste standtijden opleveren. Om de standtijd van de laselektrodes te verlengen is er wel gebruik gemaakt van smeermiddelen zoals polyisobuteen, waardoor de wrijving tussen elektrodepunt en te lassen plaat lager wordt. Hierbij dient dan wel te worden opgelet dat er geen overmaat olie aanwezig is.
Reinigen en ontvetten
Om een dergelijk laag weerstandsniveau te bereiken moet er adequaat worden gereinigd en ontvet. Ontvetten kan plaatsvinden door middel van afvegen, borstelen, sproeien of dampontvetten, dit alles met commercieel leverbare oplosmiddelen. Dit kan het best worden gedaan voor er enige vorm van mechanisch reinigen plaatsvindt. Mechanische snijranden kunnen bramen vertonen langs de rand, waarachter vuil en vet wordt vastgehouden. Deze bramen dienen allereerst te worden verwijderd door schrapen met een schraper. Gebruik nooit alleen maar een staalborstel (met roestvast-staaldraad) omdat het hiermee nooit zeker is dat alle bramen worden verwijderd. Schrapen is ook een uitstekende methode voor het verwijderen van oxidelagen. Voor dit laatste kan ook gebruik worden gemaakt van roestvast-staalwol. Er mag onder geen beding gebruik worden gemaakt van gewone staalborstels met draad van koolstofstaal, borstels met draad van messing of koper. Wees er zeker van dat alle gereedschap apart wordt gehouden voor uitsluitend gebruik voor aluminium. In bepaalde gevallen, in het bijzonder als er wordt gestreefd naar het verkrijgen van totale afwezigheid van poreusiteiten, kan chemisch reinigen of beitsen vereist zijn. Tabel 1 geeft een overzicht van een aantal chemische behandelingen om te reinigen en om oxidelagen te verwijderen.
Eenmaal ontvet en gereinigd wordt het basismetaal gelast binnen een zo kort mogelijk tijdsinterval; enkele uren is redelijk. Het werkstuk moet in een schone conditie worden gehouden gedurende deze tijd en kan voor dat doel worden afgedekt met polytheen of bruin papier. Als het werkstuk een nacht over moet staan, kan het noodzakelijk zijn om de laskanten nogmaals te reinigen. Het is dus zaak om alleen die onderdelen te reinigen die binnen een productieperiode van 4 tot 5 uur kunnen worden gelast. Er zijn nog een aantal punten met betrekking tot reinheid het vermelden waard. Als de chemische reiniging zeer goed is, dan is het mogelijk om de werkstukken gedurende langere perioden te laten staan alvorens ze te lassen, misschien wel een nacht over als de opslagcondities schoon en droog zijn. Er is ook opgemerkt dat wanneer werkstukken ‘super’ schoon zijn de TIG- of MIG-lasser boogstart- en boogstabiliteitsproblemen kan ondervinden. De reden hiervoor is niet duidelijk , maar hangt waarschijnlijk samen met de volledige afwezigheid van enig oxide. Men is van mening dat een kleine hoeveelheid oxide behulpzaam is bij de vorming van een actieve anodevlek, hetgeen resulteert in een stabielere boog. De verwerkingsafdeling voor aluminium dient volledig te zijn gescheiden van andere afdelingen. Zo kan bijvoorbeeld stof dat ontstaat tijdens schuren zich op het aluminiumoppervlak afzetten en moeilijkheden veroorzaken, vooral als zulk stof afkomstig is van het schuren van staal. Aluminium en staal mogen nooit in dezelfde lascabine worden gelast. Er kan niet genoeg op worden gewezen hoe belangrijk aandacht voor reinheid is als er goede, foutvrije lassen moeten worden gemaakt.
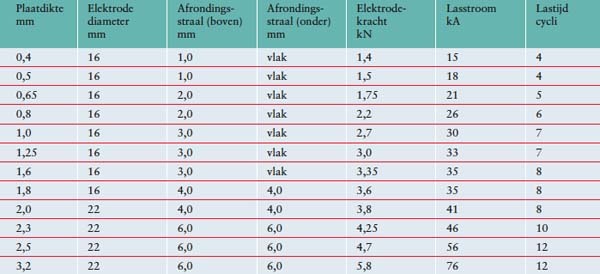
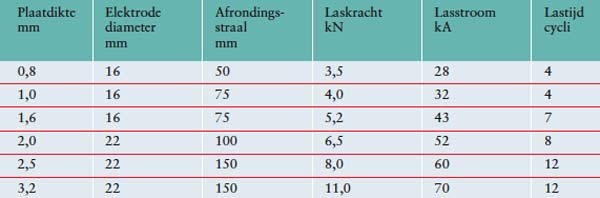
Puntlasprincipes en parameters
Van alle weerstandslasmethodes komt puntlassen het vaakst voor. De basisprincipes van de techniek worden geïllustreerd aan de hand van afbeelding 1. Er kunnen maar liefst vijf overlappende platen aluminium aan elkaar worden gelast in een lasgang. De puntlas strekt zich uit door de platen zonder het oppervlak van de buitenste platen te doen smelten. De hoofdparameters zijn de stroom, druk en tijd. Tabel 2 en 3 geven kenmerkende parameters. Het verdient aanbeveling om bij het ontwikkelen van een lasprocedure eerst de elektrode-afmetingen, lastijd en lasdruk te kiezen, waarna de lasstroom wordt opgevoerd totdat de gewenste puntlasafmetingen worden bereikt. Tabel 4 geeft minimum aanbevolen puntlasafmetingen voor de dunste van een te lassen platenpaar.
De lasdruk in geval van gebruik van een driefase frequentieomvormer is 2 tot 5 keer, die in geval van gebruik van een enkelfase wisselstroomvoeding en voor driefase secundair gelijkgerichte machines ligt bij 0,5 tot 2 keer. Er zij opgemerkt dat een buitensporige aandrukkingskracht zal resulteren in indeuking van de platen, verhoogde vervorming en plaatseparatie. Een te lage aandrukkingskracht resulteert in metaaluitstulping, verbranding van het oppervlak als gevolg van slecht contact, oppikken door de elektrodepunt of verontreiniging en inwendige defecten in de vorm van poreusiteiten en scheuren. Als er een aandrukkingskracht nodig is om te helpen bij de consolidatie van de las, dan moet deze, in het bijzonder bij scheurgevoelige legeringen, liggen bij 2,5 tot 3 keer de lasdruk. De lasstroom voor driefaseconverters moet ongeveer 30% hoger worden genomen dan die voor enkelfasige wisselstroomapparaten. Een beheerste up-slope van de lasstroom, zeg gedurende 2 of 3 cycli, maakt dat de elektrodes zich zetten op het oppervlak en daardoor metaaluitstulping beperken alsmede oververhitting van het oppervlak. Een down-slope van de lasstroom reduceert de stollingssnelheid en is behulpzaam bij het harden van de puntlas indien er na het lassen wordt verstevigd.
Laskopvereisten
De laskop kan worden gemonteerd op een voetstuk, een werktafel, een speciale machine, een met de hand bediende arm of een robot. De simpelste machine is de handbediende machine op een voetstuk maar zelfs deze kan worden uitgebreid met automatische aanvoer en uitwerping. De machines op een voetstuk zijn in staat tot het leveren van de hoogste vermogens, met capaciteiten die lopen van 5 tot 400 kVA. De draagbare apparaten zoals worden gebruikt bij robots in de automobielindustrie hebben een capaciteit van in het algemeen 10 tot 150 kVA. Het ontwerp van de laskop is belangrijk voor de reductie van elektrodepuntslijtage, is verder behulpzaam bij het tegengaan van poreusiteiten en scheuring en maakt hoge productiesnelheden mogelijk. De laskopkarakteristieken die van invloed zijn op de elektrodeslijtage omvatten de snelheid waarbij de laskop naar de lasplek toebeweegt - grotere apparatuur kan zijn voorzien van een laskop met twee snelheden die de volledige kracht ontwikkelt nadat het initiële elektrodecontact is gemaakt. Hoewel de standtijd van de elektrodepunt wordt verlengd, zal de lage naderingssnelheid de lascyclus verlengen en aldus de productiesnelheid verlagen. De traagheid van de laskop is van invloed op de mate van versnelling en vertraging en in het ideale geval moet de laskop zodanig worden ontworpen dat hij zo licht mogelijk is met voldoende stijfheid. Teveel buiging van de armen zal resulteren in verhoogde elektrodeslijtage als gevolg van beweging tussen de elektrode en het werkstuk en zal leiden tot onaanvaardbare uitlijning van de elektrode. Lage traagheid is eveneens vereist tijdens stolling van het lasbad. Als het gesmolten metaal afkoelt en stolt, trekt de puntlas samen. De elektrode moet in staat zijn om snel te reageren en moet ook in staat zijn om deze lichte vervorming te volgen willen er foutvrije lassen worden verkregen. Er wordt daarom vaak een ‘knijp’ aangelegd, die helpt bij de consolidatie van de las, waardoor krimpporeusiteiten en scheuring afnemen.
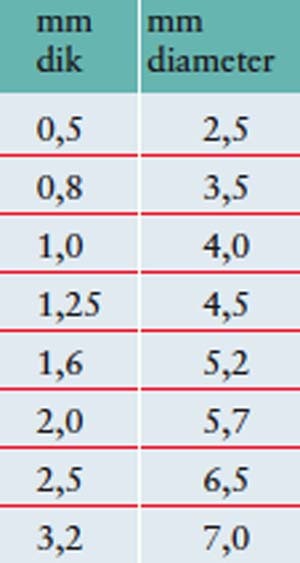
Laselektrodes
Het merendeel van de kosten van een puntlas wordt gevormd door de prijs van het slijpen of vervangen van de elektrode, waarbij de levensduur wordt gedefinieerd door het aantal puntlassen dat kan worden gemaakt met een elektrodepaar onder handhaving van een minimum puntlasdiameter. Opname van aluminium door de elektrodepunt en snelle slijtage zijn de twee hoofdredenen voor het korte leven van puntlaselektrodes. Hoge lasstroom, oppervlakteafwerking en elektrodekrachten bevorderen op hun beurt het verkorten van de levensduur van de laselektrodes. Het is niet ongewoon bij zeer hoog kwalitatieve toepassingen, zoals in de ruimtevaartindustrie, om de elektrode om de twintig lassen te reinigen. De levensduur van puntlaselektrodes kan worden verlengd door gebruik te maken van verwisselbare kapjes op de elelektrodepunt of, zoals wordt beweerd, door gebruik te maken van gelegeerd koper met verhoogde hardheid die bloemkoolvorming van de punt tegengaat. Verhoging van de hardheid kan worden verkregen door te legeren met zirconium of cadmium-chroom en door uitscheidingsharding met aluminiumoxide. Van deze varianten wordt 1% Cd-Cu-legering gebruikt voor het puntlassen van de zachtere aluminiumlegeringen en 1%Cr-Cu- of 21%Cr-Zr-Culegeringen voor het puntlassen van koudvervormde of verouderingsgeharde aluminiumlegeringen. Het profiel van de elektrodepunt is belangrijk met betrekking tot zowel de standtijd van de elektrodepunt als de laskwaliteit. Elektrodepunten kunnen kegelvormig, vlak, afgerond of cilindrisch zijn. Van deze typen komen de afgeknotte kegel en de afgeronde vorm het meest voor. De vaakst aanbevolen elektrodepunt is de afgeronde, omdat deze vorm makkelijk is te handhaven tijdens productie dan de afgeknotte kegel.
Uitlijning is van wat ondergeschikt belang en speelt alleen een rol bij draagbare apparatuur. De afgeknotte kegel wordt eigenlijk gereserveerd voor kwaliteitstoepassingen, hoofdzakelijk omdat de elektrodeuitlijning kritischer is en moeilijker te handhaven tijden productie. Standtijd van de elektrodepunt is bij afgeknotte kegelpunten beter met een factor van twee tot drie ten opzichte van de afgeronde punt. Kegelhoeken variëren van 60° tot 150° inclusief een kleine hoek aan de punt die behulpzaam is bij het uitlijnen en die markeren van de plaat beperkt. Het puntprofiel kan in stand worden gehouden door middel van slijpen, vijlen of door gebruik te maken van schuurlinnen in een voorgevormde mal. Hoewel deze bewerking handmatig kan worden uitgevoerd, is het moeilijk om een correcte puntvorm en uitlijning te handhaven. Het gebruik van automatisch gereedschap of handbediende of pneumatische puntvormers wordt ten sterkste aanbevolen. Efficiënte elektrodekoeling is eveneens noodzakelijk om de standtijd van de elektrodepunt te verlengen. Hoewel elektrodes met grote diameters aanzienlijke hoeveelheden warmte kunnen opnemen, is het gebruik van waterkoeling onontbeerlijk. Het koelkanaal moet zo dicht mogelijk in de buurt van de punt liggen. Een afstand tussen 12 en 20 mm is normaal bij waterstromingssnelheden van 5 - 10 liter/minuut. De watertemperatuur bij intrede dient rond de 20°C te liggen en bij uittrede rond de 30°C.
Kwaliteitscontrole
Er is geen specificatie beschikbaar voor de kwaliteitscontrole van aluminiumpuntlassen, hoewel de ASME IX regels bevat voor procedurekwalificatie van puntlassen. Er bestaat wel een specificatie voor het puntlassen van staal, die tal van aanbevelingen bevat die ook toepasbaar zijn op aluminium. De voornaamste methode voor het demonstreren van aanvaardbare kwaliteit bestaat uit de afpelproef. Dit is een simpele en goedkope test, die echter mogelijk wordt aangevuld of vervangen door een trek-afschuifproef of een torsieproef. Het proefstuk is in alle gevallen ongeveer hetzelfde: twee overlappende platen die aan elkaar zijn gelast met een enkele puntlas. Er is bij de afpeltest sprake van een acceptabel resultaat wanneer de puntlas uit de basisplaat wordt getrokken Het gadeslaan van de lasparameters is een effectieve methode voor het vaststellen van de kwaliteit tijdens productielassen. Dit gadeslaan kan heel eenvoudig zijn, waarbij alleen de aan- of afwezigheid van een las wordt waargenomen, maar het kan ook op zeer geavanceerde wijze elektronisch plaatsvinden met een monitor waarop de stroom, het aantal cycli, de druk en de tijd worden weergegeven. Hieraan kan nog een waarschuwingssignaal worden toegevoegd dat afgaat als bepaalde parameterinstellingen worden overschreden. Een van de effectiefste kwaliteitscontrolemethodes is nog altijd visuele inspectie waarbij oppervlaktesmelting, kleven van de elektrodes, putten, scheuren, asymmetrie van de lasspot en oppervlakte- indeuking snel kunnen worden geïdentificeerd.