Het voorkomen van porositeit en zwarte aanslag bij MIG/TIG-lassen van aluminium
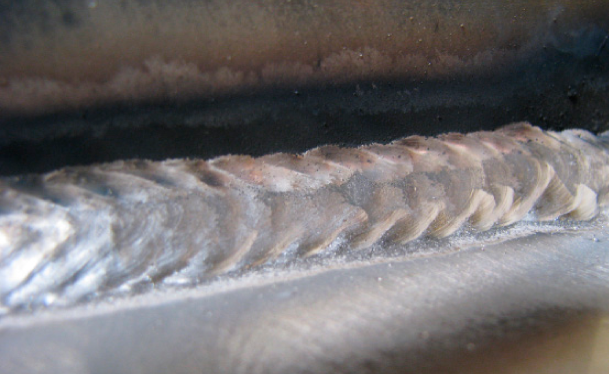
Bij het MIG- en TIG-lassen worden het smeltbad en zijn directe omgeving door de toevoeging van een beschermgas beschermd tegen de nadelige invloeden van de omringende lucht. De keuze van het beschermgas is onder meer afhankelijk van het te lassen materiaal, de oppervlaktegesteldheid, de dikte van het materiaal maar ook van het lasproces zelf. Ondanks een juiste keuze van het beschermgas blijkt bij het lassen van aluminium toch vaak dat er in de las porositeit ontstaat of dat de las en zijn directe omgeving een zwarte aanslag krijgen. Dat gebeurt vooral als gevolg van vocht.
Porositeit in aluminium wordt altijd veroorzaakt door waterstof dat in het metaal ingesloten raakt als het uithardt. De waterstof kan overal vandaan komen: uit vocht in de lucht, uit vocht in de oxidelaag op het werkstuk of uit olie en vetten op het metaal, die hydrocarbonaten bevatten. Terwijl de oplosbaarheid van waterstof in staal twintig keer toeneemt als staal vloeibaar wordt, neemt de oplosbaarheid van waterstof in aluminium zelfs met een factor 2000 toe. Dat betekent dat bij het lassen van aluminium veel meer waterstof in het smeltbad ingesloten kan raken dan bij het lassen van staal. Ook het feit dat aluminium als gevolg van een betere warmtegeleiding sneller uithardt, draagt bij aan een hogere opname van waterstof in de lasnaad. Porositeit bij het lassen van aluminium is volgens de normen in grotere mate aanvaardbaar dan bij het lassen van staal. In de EN-ISO 17637 norm staan de richtlijnen voor visuele inspectie van aluminium lasnaden en in de EN-ISO 17636 voor RX-inspectie. Toch moet men ernaar streven vocht bij het lassen van aluminium tot een minimum te beperken om tot een goede las te komen.
Voorzorgsmaatregelen
De meest effectieve manier om porositeit te voorkomen is de aanwezigheid van vocht en waterstof te verminderen voordat met het lassen wordt begonnen. In de literatuur worden diverse voorzorgsmaatregelen genoemd om mogelijke bronnen van vocht vóór het lassen te elimineren. Dat zijn onder andere:
- alle aluminium componenten moeten voor het lassen zorgvuldig ontvet en gedroogd worden
- de lasnaad en zijn directe omgeving met een roestvaststalen borstel schoonmaken of mechanisch bewerken om de oxidehuid te verwijderen, dan wel het materiaal voor het lassen te beitsen
- de aluminium delen die gelast moeten worden, zagen, knippen of bewerken zonder koelvloeistoffen te gebruiken
- zo kort mogelijk daarna (binnen 4 uur) met lassen beginnen
- een zo dik mogelijke lasdraad gebruiken omdat deze een relatief dunnere oxidehuid heeft
- toevoegmateriaal opslaan in een geconditioneerde ruimte of kast die bij voorkeur van verwarming is voorzien
- opslag van plaatmateriaal in een geconditioneerde, verwarmde ruimte
- voorverwarmen van de lasnaad- en omgeving om aanhechtend vocht te verwijderen (bij dikkere platen aan te raden)
- de lasdraad na beëindiging van de werkzaamheden niet op de machine laten zitten, maar in de verwarmde kast opslaan.
- gebruik van mechanisch geschaafde draden (tot 6 maal geschaafd)
Onderzoek heeft bovendien uitgewezen, dat het gebruik van gassen die helium bevatten (zoals Alumaxx® Plus) een groter en heter smeltbad tot gevolg heeft, waardoor het smeltbad langzamer afkoelt en uithardt. Daardoor heeft het waterstofgas meer tijd om te ontsnappen. Het voorverwarmen is een goede optie voor dikker materiaal.
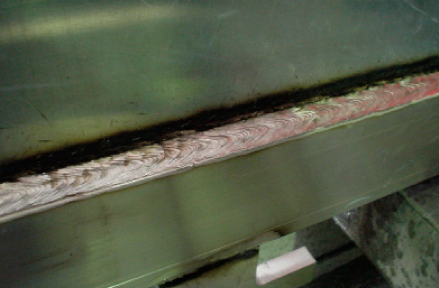
Condensatie
Het zal duidelijk zijn dat de genoemde voorzorgsmaatregelen niet altijd consequent of effectief kunnen worden uitgevoerd. En zelfs als dat wel gebeurt kan er toch altijd nog porositeit en zwarte aanslag ontstaan, zo is uit onderzoek gebleken. Het daarvoor verantwoordelijke vocht blijkt in dat soort gevallen afkomstig te zijn uit het slangenpakket. Het vocht ontstaat door condensatie van omgevingslucht in de slangen als er niet gelast wordt of door het aanzuigen van (vochtige) lucht door een lekkende toorts of lekkende koppelingen. Het vocht kan ook in de slangen komen door verschillende concentraties van vocht in de slangen en de omgevingslucht of door partiële drukverschillen in en buiten de slang. Diffusie ontstaat uiteraard alleen als het materiaal van de slangen een hoge doorlaatbaarheid (permeabiliteit) heeft. Het vocht is zeker niet afkomstig van het beschermgas zelf, dat ongeacht de samenstelling en de leveringsvorm gegarandeerd een lager vochtgehalte heeft dan 10 ppm. (parts per million). Uit metingen in de praktijk waarbij de hoeveelheid vocht aan de gascup werd gemeten, is gebleken dat vochtwaarden van zo’n 400 ppm. geen uitzondering zijn. Bij een splinternieuwe MIG-toorts die rechtstreeks uit de verpakking kwam werd zelfs een extreme waarde van 1500 ppm. vocht gemeten. Door het gasdistributiesysteem te ‘conditioneren’ kan het vochtgehalte aan de gascup aanmerkelijk worden beperkt waardoor porositeit en zwarte aanslag aanzienlijk verminderd of zelfs voorkomen kan worden.
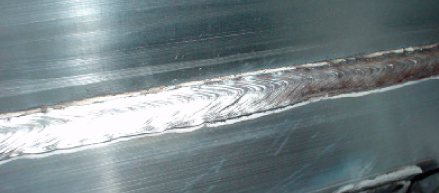
Het gebruik van slangen
Om vocht in de slangen te voorkomen kunt u het best de volgende aanbevelingen volgen:
- De slangen moeten vanwege de geringe doorlaatbaarheid gemaakt zijn van polyethyleen of rubber, en als laatste eventueel van PVC
- nieuwe slangen of slangen, die niet vaak gebruikt worden, kunnen vocht bevatten en dus een hoger vochtgehalte in het beschermgas tot gevolg hebben. Het is belangrijk om dergelijke slangen voor het lassen goed door te blazen en zeker de einden af te sluiten bij langere opslag in een magazijn
- de lastoorts en de koppelingen moeten goed gecontroleerd worden, om te voorkomen dat er lekkage ontstaat, waardoor lucht wordt aangezogen. Ook de gascup moet goed worden aangedraaid
- als de lastoorts langere tijd wordt opgeslagen, kan deze het best worden afgesloten met tape of een dop om te voorkomen dat er lucht in komt. Het verdient aanbeveling om de gasleiding & slangen ook tijdens het niet lassen continu met een laag gasdebiet (ong. 1 l/min) te spoelen om vochtindringing te beperken
- De slangen moeten in het ideale geval voor het lassen doorgeblazen worden met een inert gas, argon) of stikstof
Dit artikel is geschreven door ing. Marco Ameye (EWE), Fabrication Manager bij Air Products.