Lasbaarheid van ferritisch rvs
Vanwege de hoge nikkelprijzen mag ferritisch RVS zich verheugen in een hernieuwde belangstelling. Omdat austenitisch RVS jarenlang op vrijwel elk terrein de boventoon voerde, is de bekendheid met andere RVS-soorten wat in de vergetelheid geraakt.
A.J. Schornagel
Indeling van ferritisch RVS
Ferritisch RVS kan worden ingedeeld in groep I-legeringen, dat zijn de standaardtypen, groep II-legeringen, dat zijn aangepaste versies van de groep I-legeringen en dan de groep III-legeringen, die heel weinig interstitiële elementen (koolstof, stikstof en zuurstof) bevatten of stabiliserende elementen ter verbetering van de corrosievastheid en taaiheid in de gelaste toestand.
Groep I-legeringen
Ferritisch RVS van de 400-reeks uit deze groep is al sinds jaar en dag verkrijgbaar en wordt hoofdzakelijk gebruikt vanwege hun weerstand tegen corrosie en scalevorming bij verhoogde temperatuur. Tabel 1 geeft de chemische samenstelling van deze typen. Hoewel deze legeringen bruikbare eigenschappen bezitten in de gewalste toestand, vermindert lassen de sterkte, taaiheid en corrosieweerstand als gevolg van korrelvergroving en martensietvorming. Lassen van deze commerciële typen vereist voorwarmen en warmtebehandeling na lassen. Om die redenen is het gebruik van de 400-reeks groep I ferritisch RVS niet zo uitgebreid als mocht worden verwacht, vergeleken met de makkelijk te lassen 300-reeks austenitisch RVS.
Groep II-legeringen
Om de lasbaarheid wat te verbeteren zijn verscheidene standaard ferrieten gemodificeerd. Groep II ferritisch RVS, dat minder chroom en koolstof bevat en waaraan ferrietstabilisatoren zijn toegevoegd, is opgesomd in tabel 2. Type 405 bijvoorbeeld, bevat nominaal 12% Cr, bevat minder koolstof en er is 0,20% aluminium bijgelegeerd om austenietvorming bij hoge temperatuur te beperken, zodat harding tijdens lassen wordt verlaagd. Voor maximale corrosieweerstand en taaiheid, is gloeien na lassen noodzakelijk. Voor lassen wordt lastoevoeg-metaal van het type 430 of 309 aanbevolen, waarbij laatstgenoemde wordt gebruikt als verhoogde taaiheid van de las wordt gevraagd. Type 409 is een van de meest gebruikte ferritische RVS-typen. Deze legering, waaraan titanium is toegevoegd, wordt heel veel gebruikt voor automobiel-uitlaatsystemen en wordt vaak weerstandgelast.
Groep III-legeringen
Als er aan ferritisch RVS meer chroom en molybdeen wordt toegevoegd, dan verkrijgt het een gunstige combinatie van weerstand tegen uniforme corrosie, putcorrosie en spanningscorrosie.
Tabel 1 Nominale chemische samenstelling van representatieve groep I-standaardtypen uit de 400-reeks ferritisch RVS
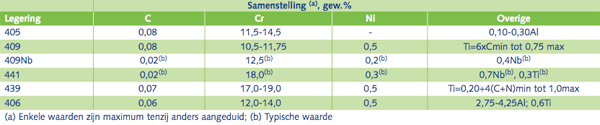
Deze eigenschappen maakt het tot een aantrekkelijk alternatief voor austenitisch RVS, dat nogal eens last had van spanningscorrosie onder invloed van chloriden. Er werd geredeneerd dat door beheersen van het gehalte aan interstitiële elementen (koolstof, stikstof) van deze nieuwe ferritische legeringen, hetzij via ultrazuivering, hetzij via stabilisering, de vorming van martensiet zou kunnen worden geëlimineerd. Alsmede de noodzaak van voorwarmen en gloeien na lassen, zodat de lassen bestand zouden zijn tegen corrosie, sterk en taai zijn in de gelaste toestand. Van meet af aan ontstonden er twee basissystemen.
Ultrahoogzuivere groep III-legeringen
Ferritische legeringen die een (C+N)-gehalte van minder dan 150 ppm bezitten, worden als ultrahoogzuiver aangeduid. Tabel 3 geeft een aantal commercieel verkrijgbare typen. Zuiverheid is vooral belangrijk bij de hoger-chroomhoudende legeringen vanwege het effect op taaiheid, sterkte en lasbaarheid. Zuurstof en waterstof zijn bijzonder schadelijk en hun gehaltes moeten zorgvuldig binnen de perken worden gehouden. Er wordt aan sommige van deze legeringen een bescheiden hoeveelheid niobium toegevoegd om de corrosieweerstand in de gelaste toestand te bewaren.
Tabel 3 Nominale chemische samenstelling van groep III ultrazuiver ferritisch RVS.
Middelmatigzuivere groep III-legeringen
Als het (C+N)-gehalte meer dan 150 ppm is, maar minder dan 800 ppm, wordt er gesproken van middelmatige zuiverheid. Legeringen, opgesomd in tabel 4, zijn commercieel leverbaar. Omdat dit staal hogere koolstof- en stikstofgehaltes bezit, is de taaiheid en sterkte inferieur aan die van de ultrazuivere legeringen. Om deze reden wordt de materiaaldikte beperkt tot een maximum van ongeveer 3 mm, waarbij de sterkte nog toereikend is. Om een aanvaardbare corrosieweerstand in de gelaste toestand te handhaven wordt er titanium en/of niobium toegevoegd om het koolstof en stikstof te binden. Die zouden anders carbiden en nitriden vormen met het aanwezige chroom, hetgeen kan leiden tot interkristallijne corrosie in bepaalde milieus. Deze vorm van aantasting wordt het vaakst waargenomen in de WBZ. Hoewel niobium en titanium beide stabiliserende elementen zijn, zijn ze niet equivalent.
Tabel 4 Nominale chemische samenstelling van groep III middelmatigzuiver ferritisch RVS.
Lasbaarheid
De term lasbaarheid geeft het gemak aan waarmee goede lassen kunnen worden gemaakt en de geschiktheid van deze lassen om met bevredigend resultaat in de praktijk te worden gebruikt. Het is daarom noodzakelijk dat lasbaarheid mechanische aspecten omvat zoals sterkte, taaiheid en kerfslagsterkte alsmede corrosie-aspecten zoals de weerstand tegen interkristallijne aantasting, scheurvormende spanningscorrosie en uniforme corrosie. De relatieve prestaties en lasbaarheid van ferritische legeringen kunnen het best worden bepaald door het kerfslaggedrag van dit staal te vergelijken. Voorts moeten kerfslagproeven op de WBZ en de las worden inbegrepen bij de kwalificatie voor zowel de lasprocedurespecificatie als de lassersbekwaamheidskwalificatie voor dit staal. Naast bepaling van de Charpy-V-kerfslagenergie (waarbij ook de bros-taaiovergang wordt onderzocht), dienen voor een grondige analyse van de lasbaarheid ook de laterale uitzetting en percentage taaie breuk van de proefstukken te worden vastgesteld. Door de jaren heen zijn er twee opvattingen ontstaan over hoe groep III ferritisch RVS te lassen. De ene beveelt aan om ze te lassen zoals ook austenitisch RVS wordt gelast en de andere is van mening dat er extra zorg moet worden besteed en het gebruik van aangepaste technieken, meer in de trant van het lassen van bijvoorbeeld van titanium. Voor groep III-legeringen is extra zorg en speciale technieken noodzakelijk. Voor het lassen van legeringen van groep I is ook speciale zorg nodig, terwijl legeringen uit groep II vrij routinematig kunnen worden gelast. De unieke eigenschappen in gelaste toestand van groep III ferritisch RVS zijn mogelijk gemaakt door het verkrijgen van hetzij zeer lage verontreinigingsniveaus, waarin zijn inbegrepen koolstof, stikstof en zuurstof (ultra-zuivere legeringen), hetzij door een zorgvuldige balans tussen niobium en/of titanium om het koolstof-, stikstof- en zuurstofgehalte te evenaren (middelmatig zuivere legeringen). Om deze redenen dient elke voorzorgsmaatregel te worden genomen en moeten lasprocedures worden gekozen waarbij de gasbescherming en reinheid optimaal zijn om opname van koolstof, stikstof, zuurstof en waterstof te voorkomen. Autogene lassen in ferritisch RVS vertonen betrekkelijk simpele microstructuren. De korrelgrootte neemt toe van de rand van de WBZ tot aan de fusielijn. In ongestabiliseerde of met niobium gestabiliseerde lassen strekken zich stengelvormige korrels uit van de fusielijn tot waar ze een welgedefinieerde middellijn tegenkomen. In met titanium of met titanium en niobium gestabiliseerde lassen, is er sprake van een kenmerkende overgang van stengelvormige korrels nabij de fusielijn naar willekeurig geöriënteerde korrels in de buurt van het midden van de las. Laatstgenoemde structuur vertoont een grotere neiging tot warmscheuren. Bij ferritisch RVS met lager chroomgehalte of hoog koolstofgehalte, zoals de typen 409, 430, 434, 442 en 446, kan er tijdens lassen martensiet worden gevormd. In de gelaste toestand kan de taai-brosovergangstemperatuur makkelijk boven kamertemperatuur liggen, wat gepaard gaat met verhoogde gevoeligheid voor lasscheuring tijdens en na afkoeling vanuit de gesmolten toestand. Voorzichtigheid is geboden bij het maken van lassen onder hoge spanning of in dikwandige werkstukken. Voorwarmen is onder deze omstandigheden een mogelijkheid om de afkoelsnelheid wat te vertragen en om spanningen die aanleiding kunnen zijn tot scheuring wat te verminderen. Een verder woord van waarschuwing met betrekking tot de selectie van voorwarm- en lasparameters: ze kunnen hogere warmte-inbreng en voorwarmen lasscheuring verminderen in sommige ferritische RVS-typen, en er kan wel korrelgroei in de WBZ optreden. Buitensporige korrelgroei kan verlies van breuksterkte, taaiheid en corrosieweerstand veroorzaken. Onder bepaalde omstandigheden kan er na het lassen worden zachtgegloeid om martensiet te verwijderen. In dat geval zullen de ferrietkorrels die al waren uitgegroeid dit nog verder doen. Zachtgloeien na lassen is in het algemeen een dure aangelegenheid, kan vervormingen veroorzaken en is te velde in het algemeen niet praktisch uitvoerbaar. Zachtgloeien van buisvormige producten in de fabriek vormt de uitzondering en wordt als standaardprocedure uitgevoerd. Dit zachtgloeien van buizen vindt plaats met hoge snelheid en wordt gevolgd door afschrikken. Ongeacht het gebruikte lasproces, zijn lasnaadvoorbereiding en grondige reiniging met een oplosmiddel dat geen residu achterlaat aan beide zijden van de naad (binnen en buiten) van het hoogste belang.
Lasprocessen
TIG-lassen
Bij het TIG-lassen dient de elektrode-negatief variant te worden gebruikt. Er wordt een wolfraam-2% thoria elektrode (AWS
classificatie EWTh-2) aanbevolen met afgeschuinde punt. Oxidatie van de elektrodepunt of opname van lastoevoeg-metaal is onacceptabel vanwege de resulterende afname van de boogstabiliteit. Als dit plaatsvindt, dan moet het lassen worden gestopt en de elektrode weer in orde worden gemaakt. Om de laskwaliteit te optimaliseren, dienen een gaslens en de grootst mogelijke keramische uitstroommond te worden gebruikt. Bij automatische processen met hogere snelheden is een nalopende beschermgasmantel aan te bevelen om mogelijke oxidatie van de las te voorkomen. Argon, helium, of mengsels van beide kunnen worden gebruikt als beschermgas. Er dient uitsluitend van hoogzuiver gas gebruik te worden gemaakt. Standaard lasgas kan inadequaat zijn vanwege cilinderverontreiniging en standaard gascilinders zijn niet gecertificeerd met betrekking tot het zuiverheidsniveau. Bij volledige doorlassing of bij het lassen van dunwandig materiaal waar oxidatie van de achterkant kan optreden, is gebruik van tegengas noodzakelijk. Bij het lassen van austenitisch RVS is het normaal om stikstof als tegengas te gebruiken (gewoonlijk om de kosten te verlagen of om het corrosiegedrag van deze legeringen te versterken). Bij het lassen van ferritisch RVS mag nooit gebruik worden gemaakt van stikstof als tegengas omdat stikstofopname ernstige verbrossing (verlies van taaiheid en sterkte) veroorzaakt. Er moet gebruik worden gemaakt van inert tegengas voor tenminste twee lagen neergesmolten lasmetaal (minimaal 3 mm). Een andere gangbare techniek die wordt gebruikt bij het lassen van austenitisch RVS is het stomp tegen elkaar plaatsen van twee stukken metaal en deze aan één kant te lassen. Hierna de achterkant schuren tot er blank metaal tevoorschijn komt en dan aan de achterkant een las leggen zodat er een volledige verbinding is ontstaan. Deze procedure moet nooit worden geprobeerd bij het lassen van ferritisch RVS, omdat mogelijk niet al het verontreinigde metaal wordt verwijderd. Er kan dan een defectieve, scheurgevoelige ferritische las ontstaan. Om laskwaliteit en prestaties te verbeteren, met name bij de groep III-legeringen, worden de volgende procedures aanbevolen:
- Grondig reinigen van de laskanten en aangrenzend metaal tot tenminste 50 mm aan beide kanten. Dit geldt ook voor het lasdraad.
- Laswerk mag alleen worden uitgevoerd met schone handschoenen. Er mogen nooit vuile, bezwete of vochtige handschoenen worden gebruikt.
- Houd de lastoorts onder rechte hoeken met het lasoppervlak binnen 15° met de verticaal om toegang van lucht in de schermgasmantel te verhinderen.
- Gaslensschermen die zijn verontreinigd met een of meer lasspetters moeten onmiddellijk worden vervangen, omdat het verbreken van de gasstroom vanuit de uitstroommond van de toorts aanzuiging van lucht veroorzaakt in de laspoel. Verwijdering van verontreinigd lasmetaal wordt aanbevolen. Gewoonlijk dient de lens te worden vervangen.
- Zwaaien van de elektrode is niet toegestaan, met uitzondering van een licht zwaaien om te komen tot goede kant-inbranding. Buitensporig zwaaien veroorzaakt contaminatie van de laspoel, met als gevolg verlies aan breuksterkte, taaiheid en corrosieweerstand.
- Tijdens lassen moet de punt van het lasdraad in de beschermgasmantel worden gehouden – een nadere reden om een gaslens te gebruiken en een zo groot mogelijke gasmond. Als de draadpunt verontreinigd raakt, hetzij doordat hij in aanraking kwam met de wolfraamelektrode, hetzij dat hij uit de gasmantel werd getrokken, moet het lassen worden gestopt. De punt van het lasdraad moet worden afgeknipt en het verontreinigde lasmetaal moet worden uitgeslepen en gerepareerd.
- Alle slangverbindingen moeten van goede kwaliteit zijn en dicht om luchtintrede te verhinderen. Alle waterafdichtingen in de toorts moeten worden gecontroleerd. Tocht in de buurt van de lasplaats moet worden vermeden om verstoring van de gasmantel tegen te gaan. De integriteit van het gassysteem moet worden gecontroleerd met behulp van een knooplasproef. Dit kan worden gedaan door een boog te trekken op een stukje plaat van hoogzuiver ferritisch RVS, waardoor er een kleine ronde laspoel wordt gevormd met een diameter van zo’n 15 mm, waarna de boog wordt gedoofd en er nog gedurende 6 seconden of meer wordt gespoeld met beschermgas. De lasknoop moet helder en glimmend zijn en vrij van aanloopkleur. Zo niet, dan moet de bron van verontreiniging worden opgespoord en verholpen.
- De toorts voorspoelen om lucht en/of vocht te verwijderen die het systeem heeft kunnen binnendringen. Bij elke lasstop moet de gasstroom nog even doorgaan om oxidatie of enige verkleuring te verhinderen.
- Er dient afstandsbediening te worden gebruikt voor het geleidelijk laten toe- en afnemen van de stroom bij het starten of doven van de boog.
- Vermijd oververhitting en verbrossing van de las door de warmte-inbreng tot een minimum te beperken en, in geval van meervoudige lassen, door de interpasstemperatuur onder de 100°C te houden.
- In geval van automatisch lassen met hoge snelheden wordt het gebruik van een nalopende beschermgasmantel aanbevolen.
MIG-lassen
Bij het MIG-lassen wordt gebruik gemaakt van elektrode-positief. De volgende methodes voor metaaloverdracht via de lasboog zijn mogelijk:
- Sproeien, dat wordt gekenmerkt door hoge warmte-inbreng en een dun-vloeibare laspoel. Bovenmatige korrelgroei is waarschijnlijk in de las en WBZ. Sproeien wordt doorgaans niet aanbevolen voor het lassen van ferritisch RVS, hoewel sommige gestabiliseerde typen minder gevoelig schijnen te zijn voor warmte-inbreng. Warmte-inbreng kan worden verminderd met het pulserend MIG-proces, zodat ook uit-positielassen mogelijk wordt.
- Globulaire overdracht wordt gekenmerkt door lagere warmte-inbreng, maar wordt meestal niet gebruikt vanwege het overmatige gespetter. Spetteren kan worden beperkt door de juiste keuze van hoogzuiver beschermgas en geschikte keuze van de energiebron.
- Kortsluitlassen, dat met de laagste warmte-inbreng gepaard gaat van alle MIG-processen. Er doen zich echter vaak fouten voor in de vorm van gebrekkige fusie, indien de juiste technieken niet worden gevolgd.
Hoewel korrelgroei tot op zekere hoogte kan worden beheerst met hogere voortgangsnelheden, lagere interpass-temperaturen en warmteputten, moet men voortdurend op zijn hoede zijn voor lasfouten zoals gebrekkige fusie en onvoldoende inbranding. In sommige gevallen kan het gebruik van austenitisch lastoevoegmetaal het probleem van korrelgroei overwinnen vanwege de vorming van een tweefasige korrelstructuur. De korrelgroei in de WBZ mag niet worden vergeten bij het gebruik van dit lastoevoegmetaal. Bij het lassen van ferritisch en austenitisch RVS met het MIG-proces met een standaard energiebron, wordt gewoonlijk geen gebruik gemaakt van zuiver argon als beschermgas vanwege booginstabiliteit, waardoor er lucht kan worden aangezogen. Dan wordt de laspoel verrijkt met stikstof en zuurstof. In de elektrode-positief toestand, zwerft de boog en zoekt plaatsen met een emissief karakter, meestal oxiden. Dit onregelmatig booggedrag veroorzaakt verstoring van de laminaire stroming van het inerte gas, hetgeen weer resulteert in aanzuiging van lucht in de gasmantel. Een manier om het boogzwerven het hoofd te bieden is toevoeging van een oxiderend element aan het beschermgas. Argon met 2% zuurstof of met 2% kooldioxide, gas dat typisch wordt gebruikt voor het lassen van koolstofstaal, laaggelegeerd staal en austenitisch RVS, wordt eveneens aanbevolen voor ferritisch RVS. Hoewel dit bevredigend schijnt voor de gestabiliseerde ferrieten uit groep II, waar het merendeel van de toepassingen ligt in uitlaatsystemen voor auto’s (type 409), mogen deze actieve, oxiderende beschermgassen nooit worden gebruikt voor de hogerzuivere ferrieten uit groep III, gestabiliseerd of niet, omdat dit gas een dramatisch nadelig effect heeft op sterkte en taaiheid. Andere onderzoekers hebben aangetoond dat het boogzwerven kan worden verholpen door een argon-helium mengsel te gebruiken, meestal 75Ar-25He, en door ervoor te zorgen dat het gas is gezuiverd en vrij is van verontreinigingen zoals lucht, vocht en koolwaterstoffen. Door te kiezen voor hoogzuiver inert gas in plaats van voor een mengsel dat reactieve gassen bevat, zoals zuurstof en kooldioxide, worden kritische legeringselementen zoals titanium, niobium, aluminium en chroom niet weggenomen door oxidatie.
Lassen met gevulde draad
Lassen met gevulde draad verloopt ongeveer net als MIG-lassen, behalve dat in plaats van een massieve draad nu een omhulling wordt gebruikt die is gemaakt van koolstofstaal, RVS of nikkel. De draad is gevuld met een kern bestaande uit legeringselementen in hoeveelheden die overeenkomen met de gewenste lassamenstelling. Sommige gevulde draadsoorten bevatten actieve fluxmiddelen, terwijl andere die niet bevatten. In sommige gevallen bevelen draadfabrikanten het gebruik aan van een beschermgasmantel en soms is het draad zelfbeschermend. Het is belangrijk om de verwerkingskarakteristieken van het draad te kennen en om te weten wanneer er beschermgas moet worden gebruikt, hetgeen betere resultaten geeft. De voordelen van het gebruik van beschermgas, zoals besproken bij MIG-lassen kunnen ook hier gelden. Het lassen met gevulde draad is niet aan te bevelen voor groep III ferritisch RVS omdat het moeilijk is om de zuiverheid van de legering te handhaven en vanwege de opname van koolstof, stikstof en zuurstof. Lassen die zijn gelegd met gevulde draad zijn nooit zo zuiver als die, welke zijn geproduceerd met massieve draad onder beschermgas. Voor minder kritische toepassingen of waar een austenitisch lastoevoegmetaal kan worden gebruikt, kan lassen met gevulde draad mogelijk zijn. Omdat er wordt gelast in het sproeigebied, is er sprake van hogere warmte-inbreng, waardoor korrelgroei op de loer ligt.
Lassen met beklede elektrode
Bij het lassen met beklede elektrode wordt de elektrode-positief toestand gebruikt. Lassen die zijn gelegd met dit lasproces zijn nooit zo sterk als die, welke zijn gelegd met een proces onder beschermgas. Om die reden zijn er geen beklede elektrodes met overeenstemmende samenstelling beschikbaar voor groep III ferritisch RVS. In feite is er sprake van een zuiverheidsprobleem, omdat koolstof, stikstof en zuurstof moeilijk zijn te weren zonder de operationaliteit van het proces al te zeer te hinderen. Daar waar beklede elektrodes beschikbaar zijn, is correcte opslag essentieel om elke vorm van vochtopname te verhinderen. Onjuiste opslag, gevolgd door vochtopname leidt gewoonlijk tot lasporositeit en in sommige gevallen tot waterstofscheuring. Voor RVS dat moet worden gebruikt in de gelaste toestand en waar zachtgloeien na lassen niet praktisch of economisch is, kan een niet-overeenkomende elektrode worden gebruikt. De keuze hierin varieert van hoog-chroomhoudende austenitische type zoals E310 of E310 ELC (die volledig austenitisch zijn) tot een hoog-nikkelhoudende legering zoals ENiCrFe-2. E309-beklede elektrode (lassen bevatten ferriet voor weerstand tegen warmscheuring) en zijn laag-koolstof en hoger-silicium varianten zijn naar volle tevredenheid gebruikt. Hooggelegeerd austenitisch lasmetaal vloeit niet zo makkelijk als ferritisch RVS. Lasmetaal met een hoog nikkelgehalte is bijzonder dikvloeibaar, met geringe penetratie. Dit gedrag vereist dat de lasser boogkracht gebruikt en elektrodemanipulatie om de laspoel fysiek tegen de laskanten aan te duwen. Ferritisch RVS heeft aanzienlijke hogere smelttemperaturen dan austenitisch RVS en corrosievaste nikkellegeringen. Als er gebruik wordt gemaakt van austenitisch lastoevoegmetaal om ferritisch basismetaal te verbinden, dan moet er voor worden gezorgd dat er voldoende warmte wordt toegevoerd om het ferritische basismetaal aaneen te laten vloeien, anders ontstaan er lasfouten in de vorm van gebrekkige fusie. Afhankelijk van het lasprofiel, kan slakinsluiting een probleem opleveren met sommige beklede elektrodes. Als de slak niet vlot lost, dan is slijpen noodzakelijk. Proberen om slakresten uit te drijven met behulp van opvolgende lasgangen heeft zelden succes. Het nettoresultaat is meestal slakinsluiting, die goed te zien is bij radiografische inspectie. Bovendien kan tussentijds slijpen resulteren in meer warmte-inbreng met als gevolg meer korrelgroei. Alles bij elkaar kan er verlies van sterkte en taaiheid optreden in de WBZ. Bij het lassen van ferritisch RVS met beklede elektrodes worden de volgende technieken aanbevolen:
- Net als bij alle andere lasprocessen moeten de te lassen oppervlakken aan beide zijden zorgvuldig worden gereinigd om vuil, vet, olie enz. te verwijderen.
- De boog moet worden gestart op de afschuining van laskant en niet op het aangrenzende basismetaal.
- Er moet een korte boog worden gehandhaafd om vorming van porositeiten te vermijden en om oxidatie-effecten en opname van zuurstof en stikstof tot een minimum te beperken.
- De elektrode moet een hoek met de verticaal maken van niet meer dan 20°.
- Licht zwaaien van de toorts is toegestaan, zolang de zwaai niet meer is dan drie keer de diameter van de kerndraad.
- Kraterscheuren bij lasstops moeten worden uitgeslepen alvorens verder te gaan.
Weerstandslassen
Puntlassen, naadlassen en flitslassen zijn te gebruiken zolang het verlies aan sterkte aanvaardbaar is. Waar mogelijk moet gebruik worden gemaakt van argon beschermgas om de lasnaad (inclusief de achterkant) te beschermen tegen oxidatie en opname van stikstof. Met titanium gestabiliseerde typen schijnen beter bestand te zijn tegen de effecten van stikstofopname tengevolge van matige afscherming dan de hoogzuivere typen. Dit is kennelijk het gevolg van de vorming van een beschermende TiN-film die de laspoel afdekt.
Plasmalassen
Plasmalassen van ferritisch RVS komt sterk overeen met TIG-lassen en dezelfde voorzorgen en aanbevelingen gelden. Men moet net als bij TIG-lassen, voorzichtig zijn met het gebruik van waterstofgas bij plasmalassen. Er kan direct na het lassen verbrossing van het staal optreden. Het merendeel van de waterstof diffundeert binnen 48 uur na het lassen het staal uit, waarna de taaiheid weer is hersteld. De situatie is kritischer bij typen met hogere chroomgehaltes. Een voordeel van plasmalassen is het ontstaan van een zeer smalle WBZ en diepe penetratie, smaller en dieper dan bij het TIG-proces. Er zal dus ook minder korrelgroei in de WBZ optreden dan in geval van TIG-lassen.
Overige lasprocessen
Ferritisch roestvast is makkelijk te lassen met het elektronenstraalproces onder hoogvacuüm. Wrijvingslassen en laserstraallassen zijn eveneens bruikbaar. Indien mogelijk, dient de laspoel te worden beschermd met een gasmantel. Onder-poederlassen kan worden toegepast voor het verbinden van ferritisch RVS, maar de hoge warmte-inbreng die met dit proces gepaard gaat, brengt ongewenste korrelgroei met zich mee in de WBZ. Opmenging kan meer dan 50% bedragen. Onder-poederlassen is ongeschikt voor de groep III-legeringen en eigenlijk ook niet geschikt voor de meeste andere legeringen.