Toepassingen van de lasercladtechnologie
Het lasercladden is interessant voor onderdelen die onderhevig zijn aan slijtage, corrosie, aantasting bij hoge temperatuur enz. Doorgaans zijn dit vitale onderdelen van machines en procesinstallaties, vervaardigd uit kostbare materialen of halffabrikaten, waaraan hoge eisen ten aanzien van betrouwbaarheid en levensduur worden gesteld.
Door ir. Wim Husslage, NedClad Technology B.V.
NedClad is in Nederland pionier bij de industriële toepassing van de lasercladtechnologie. Met deze techniek kunnen sporen of lagen door middel van overlappende sporen van metaal worden aangebracht op een metalen ondergrond. Hierbij wordt met een gefocusseerde laserbundel toevoegmateriaal in de vorm van draad of poeder gesmolten, waardoor een 100% dichte en een door smelthechting verkregen laag wordt verkregen. Bepalend voor het praktische gebruik zijn de lasmetallurgie en de gewenste eigenschappen van het werkstuk, en of die met toevoegmateriaal kunnen worden verkregen. De belangrijkste toepassingen bevinden zich waar een verbetering van de slijt- en/of corrosievastheid van belang is. Slijt- en/of corrosievaste lagen worden, zowel op nieuwe producten als op versleten of aangetaste producten, als onderdeel van de reconditionering aangebracht. Daarnaast bestaat 20 - 25% van de lasercladactiviteiten van NedClad uit het herstel van bewerkingsfouten; werkstukken die niet goed zijn gedraaid of gefreesd, zoals een verkeerde plaats van groef of spiebaan, beschadigde schroefdraad of te dunne wand. Door de kosten die met de uitvoering van het lasercladden gemoeid zijn, komen met name werkstukken met hoge toegevoegde waarde in aanmerking. Door de perfecte eigenschappen die met lasercladden kunnen worden verkregen en door de relatief geringe warmte-inbreng waarmee het proces wordt uitgevoerd, begint het lasercladden een belangrijke plaats tussen de andere (dikke laag) coatingtechnieken in te nemen. Elke techniek heeft zijn specifieke toepassingssgebied; het lasercladden geeft hier een uitbreiding aan.
De praktijk
Het lasercladden wordt uitgevoerd met een CW Nd:YAG-laser met maximaal uitgangsvermogen van 2 kW. De laserbundel wordt vanaf de laserbron via een 0,6 mm dikke glasvezel naar het optiek gevoerd. Door gebruik van verschillende optieken wordt met een ronde spot met homogene energieverdeling tussen 0,6 en 5 mm gewerkt en met een werkafstand tussen 200 en 800 mm. Het poeder wordt vanuit een poedertoevoerapparaat in een smalle bundel op de plaats van de laserspot gericht. NedClad werkt hierbij met zowel een laterale (van opzij) als coaxiale poeder-toevoer. Vanwege de grote inzetbaarheid en de grotere toegankelijkheid voor moeilijk bereikbare plaatsen wordt meestal met een laterale poedertoevoer geclad (afbeelding 1). Het optiek dat tezamen met de poedernozzle de cladkop vormt, wordt met een 6-assige robot t.o.v. het werkstuk bewogen. Voor de manipulatie wordt over een aantal manipulatoren beschikt die afhankelijk van de vorm, grootte, gewicht en te bewerken oppervlak van het te cladden werkstuk, kunnen worden ingezet. De robot kan op een track over 3 m in langsrichting worden bewogen en de robotbeweging kan worden gesynchroniseerd met de draai- en kantel-beweging van één van de manipulatoren. Lasercladden is een nog weinig bekende techniek. NedClad is één van de weinige bedrijven die het lasercladden als toe-leverancier aanbiedt en constateert een gezonde toe-na-me in de belangstelling. Belangrijkste toepassingen zijn, zoals gezegd corrosie en/of slijtvaste lagen.
Afbeelding 1 Inwendig lasercladden van afsluiteronderdeel met Inconel 625; uitwendig geclad met Stellite 21.
Staal, corrosiebescherming, zeewater
Voor heel veel verschillende toepassingen is staal hét constructiemateriaal. In een natte en corrosieve omgeving dient staal echter beschermd te worden. Of er dient een constructiemateriaal gekozen te worden dat tegen de aantasting door corrosie bestand is. Aanleiding voor de oprichting van NedClad was de vraag van de NAM om de mogelijkheid te onderzoeken om, door pitting aangetaste afdichtingsvlakken van onderdelen van afsluiters op het Groninger aardgasveld als gevolg van spleetcorrosie, te reconditioneren. Het onderzoek van opsteller, ten tijde van zijn detachering namens TNO bij de Universiteit Twente, leidde tot een gekwalificeerde herstelprocedure. Inmiddels worden voor de NAM niet alleen door corrosie aangetaste onderdelen gereconditioneerd. Ook de delen die bloot staan aan wrijving, erosie en andere vormen van slijtage worden geclad. In veel gevallen leidt dit tot producten die beter zijn dan ze ooit zijn geweest. Voor constructiestaal kunnen afhankelijk van de omstandigheden een groot aantal beschermmogelijkheden in aanmerking komen. Echter, onder zeewateromstandigheden en zeker op het grensvlak van zeewater en lucht is de aantasting het sterkste en is het aantal mogelijkheden om tot een duurzame bescherming te komen beperkt.
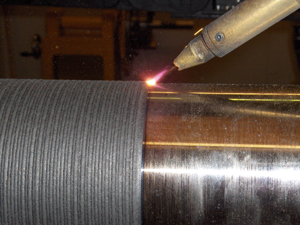
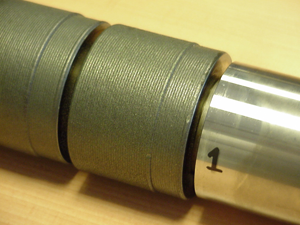
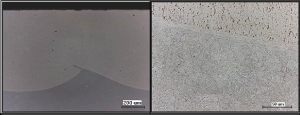
Afbeelding 3 Metallografische doorsnede van Inconel 625 lasercladlaag op staal. Links: laag na nabewerking. Rechts: smeltlijn, overgang cladlaag/werkstukmateriaal.
Bescherming van staal tegen zeewater
In 2004 werd NedClad gevraagd aan een onderzoek mee te werken, dat TNO in opdracht van Rijkswaterstaat zou uitvoeren, waarbij een groot aantal coatings op hun duurzaamheid in zeewater getest zouden worden. TNO en Rijkswaterstaat hebben daartoe op basis van de toegepaste deklagen in zeewater en potentieel interessante deklagen een aantal deklagen en een corrosievast bulkmateriaal geselecteerd. Er zijn veel materialen, die daartoe als lasercladlaag in aanmerking zouden kunnen komen. De beste resultaten worden van Ni-basislegeringen verwacht.
Bescherming van staal door lasercladden
NedClad heeft inmiddels ruimschoots ervaring opgedaan met het aanbrengen van een groot aantal verschillende corrosievaste materialen, zoals:
- AISI 304, 310 en 316
- AISI 410, 420 en 430;
- Inconel 625 en div. Hastelloys;
- NiCrBSi-legeringen;
- Ti en Ti-legeringen;
- CuNi-legeringen en Al-brons;
- Co-basislegeringen, die met name vanwege de slijt-vastheid worden toegepast, maar die door het hoge Cr-gehalte, soms gelegeerd met Mo, ook zeer corrosievast kunnen zijn.
Doordat uiteindelijk slechts één lasercladlaag in het onderzoek getest kon worden, is gekozen voor een lasercladlaag op basis van Inconel 625. Afbeelding 2 toont het lasercladden van het proefmateriaal en in afbeelding 3 een metallografische doorsnede van de cladlaag. Inconel 625 (samenstelling: < 0,05% C; 4% Fe; 21% Cr; 8% Mo; 3,5% Nb/Ta; 0,25% Al; rest Ni) heeft voor vele milieus, incl. zeewater, een grote weerstand tegen aan-tasting. Daarnaast komt het vanwege de goede kruipsterkte voor hoge temperatuurtoepassingen in aanmerking. NedClad voert het lasercladden uit met minimale opmenging van het toevoegmateriaal met het werkstukmateriaal. Op de smeltlijn is de opmenging ca. 15 - 20% en neemt snel af naar minder dan 5%, dat al op een afstand van 0,3 - 0,4 mm vanaf de smeltlijn wordt bereikt. Indien op de 1e laag nog een 2e laag zou worden aangebracht, zou nagenoeg de samenstelling van het toevoegmateriaal worden bereikt. In afbeelding 4 wordt hiervan een voorbeeld getoond voor het lasercladden van een Hastelloy-legering op AISI 316L.
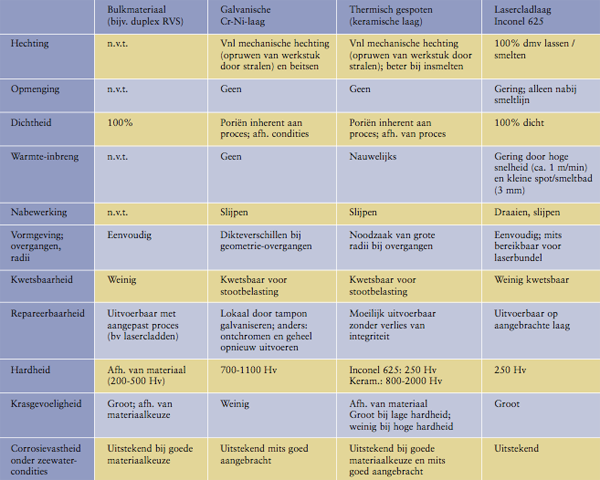
Onderzoek van beschermlagen op staal
Het door TNO uitgevoerde onderzoek omvatte een slijtage-onderzoek en een corrosieonderzoek, toegespitst op het vaststellen van de permeabiliteit van de lagen en corrosie-beproeving onder extreme condities, om extrapolaties over het langetermijngedrag mogelijk te maken. Hierbij zijn naast bovengenoemde lasercladlaag van Inconel 625 galvanische CrNi-coatings, thermisch gespoten metallische en keramische en combinaties van beide getest. Van alle geteste metallische deklagen blijken meerdere deklagen bij een extrapolatie naar 25 jaar weinig tot geen aantasting te geven. Deze coatings zouden in principe voor toepassing in aanmerking kunnen komen. Gebleken is dat niet alleen het type coating van belang is, maar ook de kwaliteit waarmee de coating is aangebracht.
Basisvoorwaarden
Belangrijke basisvoorwaarden bij de toepassing van coatings zijn:
- de dichtheid in verband met de permeabiliteit;
- de hechting in verband met de stootvastheid en niet-toelaatbare ondercorrosie;
- de warmte-inbreng in verband met mogelijke vormverandering bij de applicatie;
- de repareerbaarheid als gevolg van beschadigingen door onvoorziene omstandigheden;
- beperkingen bij de vormgeving van de constructie.
In onderstaande tabel worden een aantal belangrijke beoordelingscriteria voor respectievelijk bulkmateriaal, galvanische Cr-Ni-lagen, thermisch gespoten (keramische) lagen en lasercladlagen van Inconel 625 met elkaar vergeleken.
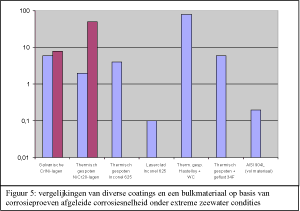
Bij de beoordeling van de corrosieweerstand bedient men zich van elektrochemische beproevingen ter bepaling van de permeabiliteit en de galvanische werking. De permeabiliteit mag zowel bij momentopname als bij langeduuronderzoek niet aanwezig zijn en het materiaal moet zich passief blijven gedragen. Uit langeduuronderzoek kan de gevoeligheid voor putvormige corrosie (pitting), spleetcorrosie en de algemene aantasting, waaruit de corrosiesnelheid kan worden afgeleid, worden beoordeeld. In afbeelding 5 worden de resultaten weergegeven, die voor de corrosiesnelheid zijn afgeleid voor een beproeving onder zeer zware gesimuleerde condities. De minste corrosie toont de lasercladlaag van Inconel 625.
Overzicht
Detail. Afbeelding 6 Lasercladden van gegoten pomponderdeel met Inconel 625.
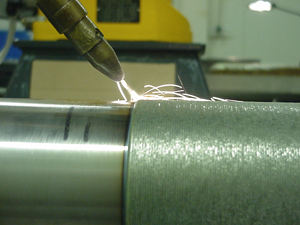
Pluspunten van Inconel 625 als lasercladlaag
Samenvattend kunnen de pluspunten van Inconel 625 als lasercladlaag ten opzichte van deklagen die door middel van galvanische, thermischgespoten en booglas-oplasprocessen zijn aangebracht, worden aangegeven:
- 100% hechting op basis van smelten met slechts geringe opmenging met het basismateriaal (alleen de onderste zone van de cladlaag);
- 100% dicht; porie- en scheurvrij;
- relatief weinig warmte-inbreng, waardoor de warmtebeïnvloede zone minder dan 0,4 mm is en ontlaten mogelijk is door een goede keuze van de bewerkingscondities;
- aan te brengen op radii en scherpe overgangen;
- aan te brengen op moeilijk toegankelijke plaatsen;
- laagdikte kan variëren tussen minder dan 0,1 tot enige millimeters;
- beschadigingen zijn repareerbaar zonder verwijdering van oude laag.
Onderstaand enige voorbeelden van werkstukken die door middel van lasercladden van een corrosievaste laag zijn voorzien. Naast Inconel 625 past NedClad met succes ook andere toevoegmaterialen voor corrosiebescherming toe. Veel ervaring is opgedaan met AISI 316, Ultimet en Hastelloy’s. In het geval dat ook hoge eisen aan de slijtvastheid worden gesteld, wordt in overleg met de gebruiker o.a. Stellite 21 of Stellite 6 toegepast of corrosievaste materialen die gemengd zijn met keramische deeltjes, waarvan NiCrBSI met globulair wolframcarbide een voorbeeld is.